SCAN for GP is the Warehouse Management Module for Great Plains that allows you to:
- Gain visibility to inventory as it moves through the warehouse
- Add scanning to the warehouse process to eliminate errors
- Update data real-time with scanning mobile computers to reduce data entry
- Integrate directly into Great Plains

Software Features
- Barcoded Real Timer Inventory (not batch or sync)
- Item / SKU Master Records
- Inventory Location Management
- RF/Mobile Computer Physical Inventory
- Standard, Ad Hoc and Query Based Reports
- Data Export to Excel and other Standard Applications
- Inventory Tracking
- LOT Number, Serial Number, Created on Date Tracking
- Barcode Printing and Scanning
- Create and Receive Inventory against POs
- RF/Mobile Computer Receiving
- Directed Put Away
- Warehouse Zoning / Directed Picking and Putaway Paths
- Directed Cycle Counting
- Create Sales Orders / Pick Tickets for Sales Orders
- Automated Inventory Allocation to Sales Orders (FIFO)
- Pick Ticket Waving / Grouping
- Batching Multiple Orders to be Picked at Once
- Standard RF/Mobile Computer Picking
- Packstation Scan Packing Verification
- Interface with UPS Worldship
- Interface with Multi Carrier Shipping System (3rd party)
- Manage LTL and Full Truck Loads
- Standard Integration to Microsoft Dynamics Great Plains ERP
- Purchasing / Receiving
- ERP Integration Module / Toolkit
- Advanced Loading Rules Based Engine
- Advanced Configuration Settings and Rules
- Advanced Inventory Allocation Rule Engine (FIFO, FEFO, Serial)
- Advanced Rules Based Waving, Batching, Cubing and Cartonization Engines
- Advanced RF/Mobile Computer Picking
- Advanced RF/Mobile Order Consolidation
Certifications
SCAN for GP is developed by a Microsoft Certified ISV Partner
Screen Shots


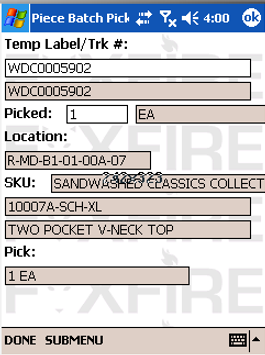
Scanners (mobile computers), Printers & Labels
Xceliware in conjunction with our partners is able to lead you through the process of selecting and integrating the "hardware" that goes into running a Warehouse Management System. This includes scanning mobile computers, wireless access points for the warehouse, pulling cable, labels and label printers, etc. While our clients are free to obtain this equipment on their own, most ask us to lead this portion of the project as well so to avoid having to coordinate multiple vendors.

Implementation Approach
Xceliware utilizes a tried and tested implementation methodology, known as Phase5 to guarantee a successful delivery of your solution to your end-users. This methodology, while tuned to meet the needs of data collection functionality, is based on IEEE Standards and incorporates a variety of industry best practices while focusing on the clients’ needs.
These 5 Phases are:
- Plan
- Design
- Implement
- Test
- Deploy
Xceliware will work with your project team to document requirements and assist in the implementation of standard and customized transaction sets into a “Conference Room Pilot” environment for testing. A complete solution requirements document will be jointly created, and design of the process flow and transaction sets will begin.
Xceliware will provide technical resources to perform the initial installation of software into your server environment, as well as assist with configuration and network issues. This will allow the implementation of a “development” server to allow for the project team to develop and test basic processes in a protected environment. Key users will be involved in this testing process to ensure acceptance by the eventual users of the system.
Following the completion of testing and training, our consulting staff will assist in the roll out of the solution in the CRP environment and into the initial facility. A plan will then be developed to assist in developing an appropriate plan for the implementation of the solution in conjunction with the rollout to the other locations. Performing the initial installation process in this fashion will expedite the training and conversion process, and allow the most cost effective use of Xceliware and your resources.
Professional Services
Xceliware's internal team and partners are the best in the business. If it relates to Supply Chain Management, Barcoding, RFID, Scanners, Software or anything in the Data Capture Industry, there is a great chance we will be able to help you.
Some of the most common services that we provide to our customers include:
Wireless Site Surveys - We will help you map your environment and identify how many wireless acces points are needed to make your environment wireless enabled.
Scanning Trouble Shooting - If your scanners are not scanning properly (maybe there is a delay) we can help you identify the problem.
Software / System Analysis - Looking for a new Supply Chain Software solution. We can help you evaluate your options and inform you of the pros and cons before you make the large investment.
Hardware / Technology Analysis - Before buying scanning devices, allow us to help you ensure that you have made the right selection.
Warehouse Labeling - Implementing a new tracking system? Let us help you design the workflow and label your assets/inventory.
Warehouse Sign Installation - Companies are amazed at the efficiencies gained by implementing an orderly workflow and properly labeling the rows & aisles in their warehouses.
Custom Software Development - Many companies know what functionality they seek from a software solution, but can't seem to find the exact fit. We can take your desires and build them into a software solution for you. This does not have to take long or be expensive.
Workflow Design & Consulting - With thousands of warehouse visits under our belts, we can help you design a better workflow.
Training - Need help getting your workforce up to speed? We can train your team.
Implementations - Already know where your going, but need help getting it done? We can get it done for you.